Key Solutions Group awarded manufacturing grant
The Queensland Government has awarded Key Solutions Group a $500,000 grant through the Manufacturing Hubs Grant Program.
The Manufacturing Hubs Grant Program provides funding and other assistance to help regional manufacturing small-to-medium enterprises build their advanced manufacturing capability.
Key Solutions Group will use the grant to purchase and install two Motoman AR1440 series welding robots, Power-Trac seam finders/trackers and rotary screw compressors.
The machinery is expected to reduce production costs by 30 per cent and generate private sector investment of more than $1.2 million.
It is also set to expand Key Solutions Group’s manufacturing capacity through the creation of eight new jobs while upskilling 28 current employees.
The funding given to Key Solutions Group was part of the Manufacturing Hubs Grant Program’s third round.
“Every time we see a Queensland manufacturer take advantage of these grant programs, I know that it’s a step in the right direction for creating a more resilient and robust manufacturing sector,” Queensland Manufacturing Minister Glenn Butcher said.
“We have helped so many businesses throughout Queensland, just like Key Solutions Group, with leaders who can see an opportunity to expand their factory’s capabilities, an opportunity to secure more clients and grow their business.
“We have heard from many manufacturers that it’s challenging to recruit staff for welding roles and so wherever possible, automation is solving some of those problems. It also means staff can be upskilled to new roles and some of those manage the robotic part of the process.”
Key Solutions Group managing director Frank Attard said the grant will assist in the growth of the company.
“We’ll be able to achieve significantly greater efficiencies in time usage and labour output, which will ultimately result in better service to our growing customer base,” Attard said.
“The robotic manufacturing facility project will be a key ingredient in our business growth path and we’re looking forward to bringing in more customers with a broader product and service offerings.”
Key Solutions Group is an engineering specialist company based in Mackay that specialises in pipe welding, repairs and component manufacturing and is a major service provider to Mackay’s mining and agriculture sectors.
Source: https://www.australianmining.com.au/key-solutions-group-awarded-manufacturing-grant/
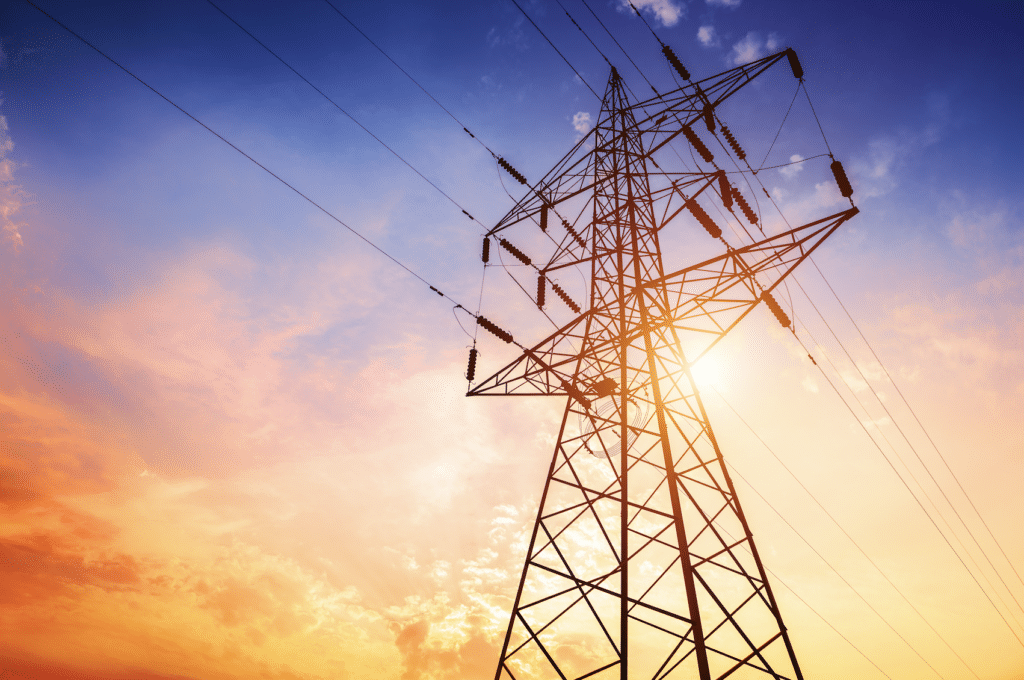
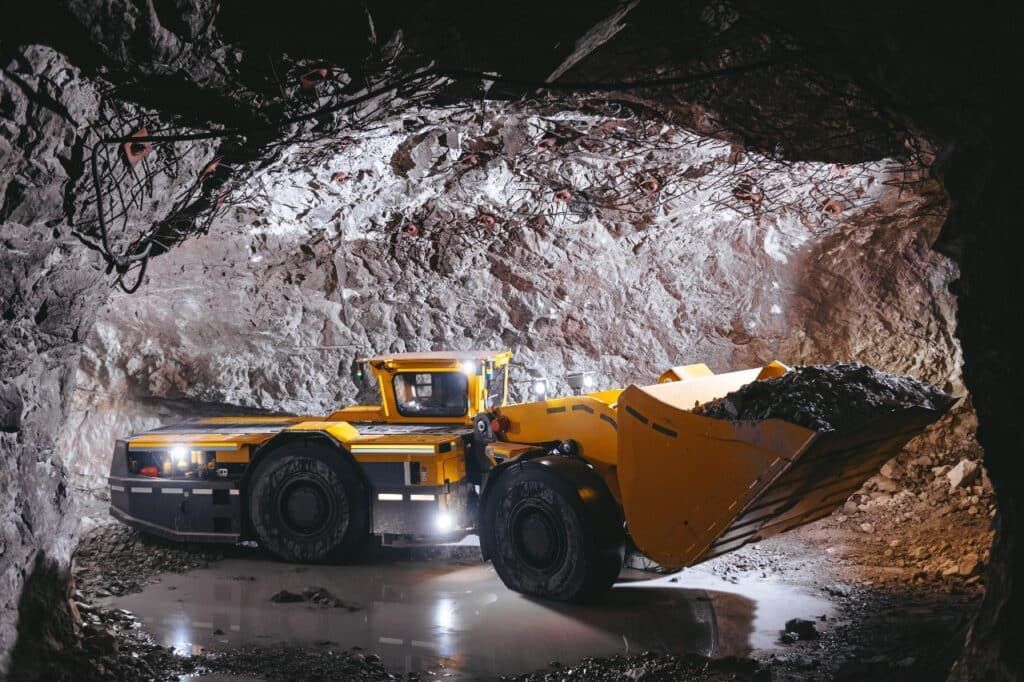
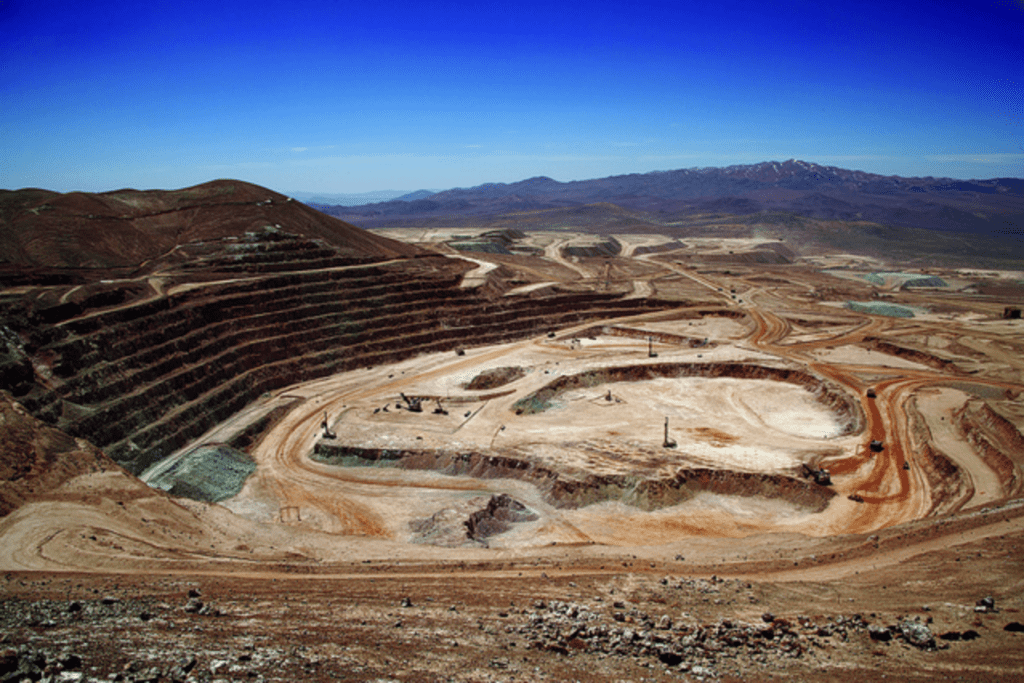